About DSB Technologies
Decades of Metallurgical Innovation
For over 40 years, we have been on a mission to change the way powder metal parts are manufactured.
DSB Technologies traces its roots back to the production of porous metal components as the Panoramic sintering division of the Parker Pen Company. Our job was to convert fine, loose particles of metal into solids through the application of heat and pressure. Few people realize how much work goes into crafting high quality writing instruments!
In 1980, Parker Pen sold the sintering division to a group of investors who formed SSI Technologies. This is where SSI Sintered Specialties began its long history of manufacturing innovation and developed a global reputation for engineering functional, high performance powder metal components.
Four decades later, SSI Sintered Specialties underwent a rebranding effort to reflect the organization’s focus on new technologies. While the company was renamed DSB Technologies, it carried on with the same enthusiastic ownership and vision for a transformative manufacturing landscape with new metallurgical solutions.
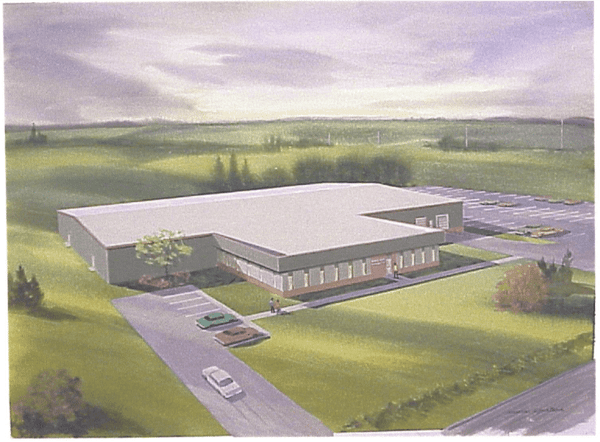
Parker Pen Building - 1977
Your Metallurgical Solutions Partner
With unmatched metallurgical expertise and a diverse technology portfolio, we have a proven history of finding new ways to manufacture highly complex, functional powder metal components for serial production.
Our forming technology portfolio, which includes Powder Metallurgy Press and Sinter, Metal Injection Molding, and Metal Binder Jetting, enables manufacturers to design complex powder metal components for high volume production through processes that had previously been economically impossible.
Complementing our forming technology portfolio is our vast range of metallurgical expertise, from custom material development to a fleet of secondary machining centers. This knowledge, coupled with over four decades of experience, provides customers with an end-to-end manufacturing partner for the design and production of powder metal components.
From SSI to DSB Technologies
In May 2022, SSI Sintered Specialties changed its name to DSB Technologies to reflect our commitment to developing innovative new processes in metallurgy. Reinventing the way powder metal parts are designed and engineered remains our mission.
This commitment to collaboration and the creation of forward-thinking, dynamic processes is reflected in our new logo. The d and b symbolize the nature of collaborative partnerships, while the s represents the journey involved in that process.
Our logo deliberately omits any straight paths, reinforcing our vision to provide dynamic solutions-based processes that are unique to every customer.
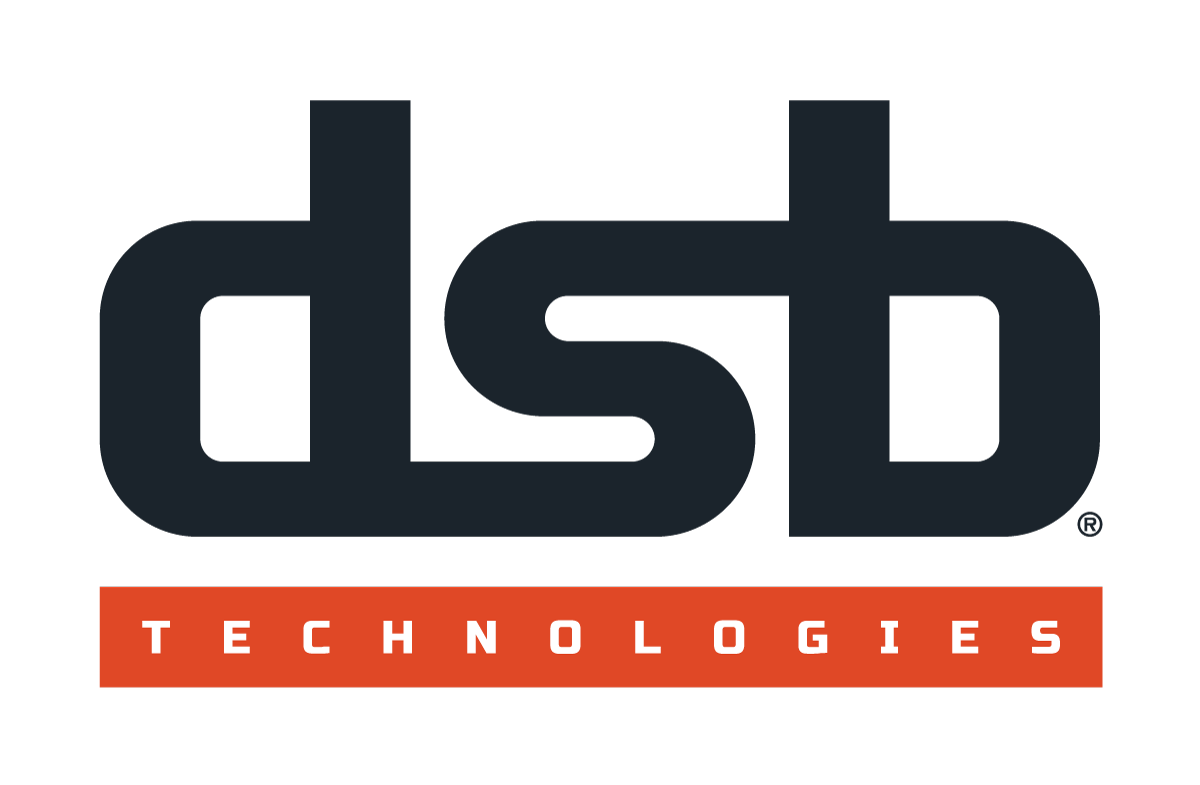
Collaborate. Discover. Innovate.
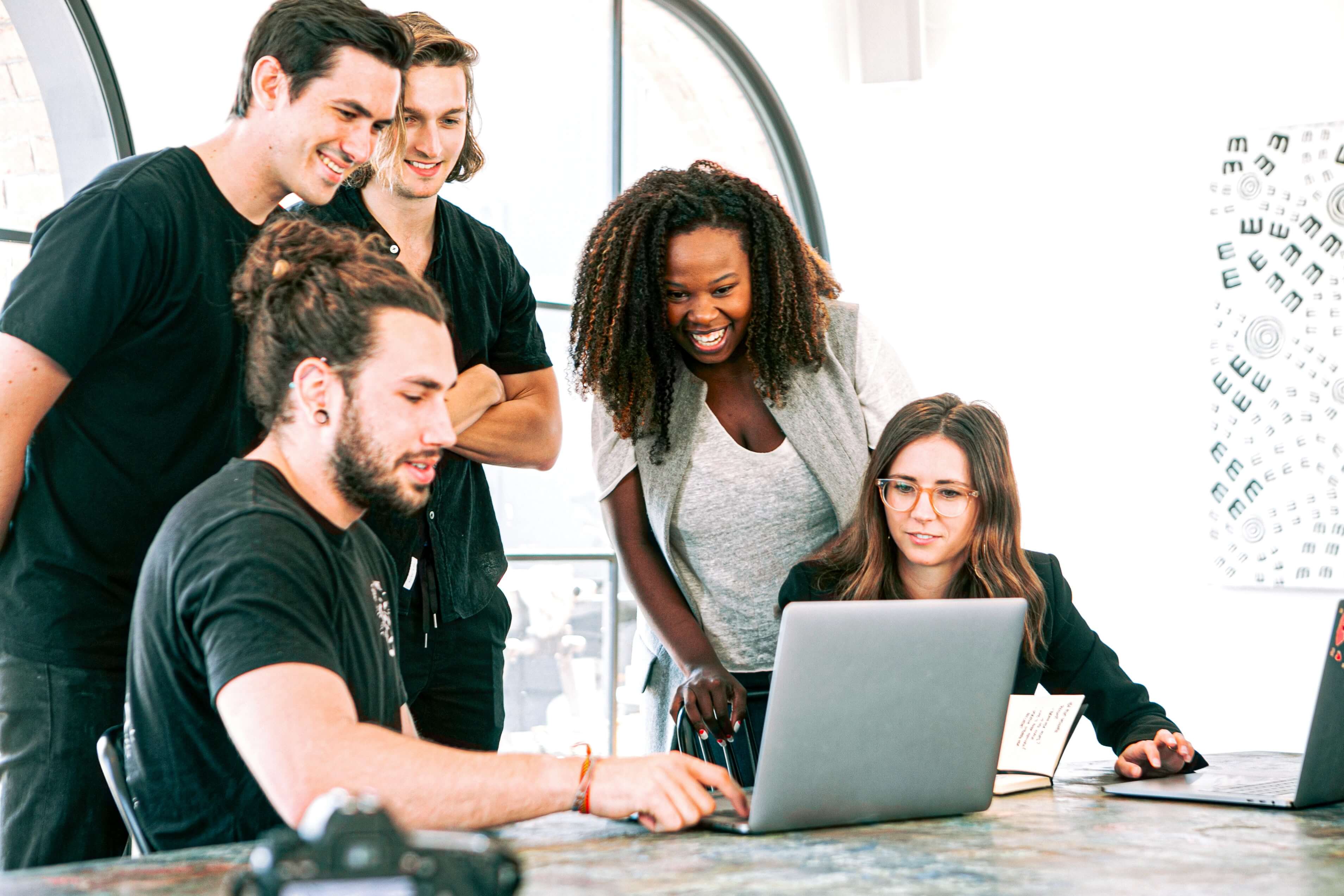
Work at DSB Technologies
We believe every successful company is powered by its employees and have created an environment that allows our team to grow with us. Whether you are looking to apply your skills to our production team or advance your career with our corporate staff, we will guide you in achieving your full potential. When you succeed, we succeed – so let’s get started together!